Calcium
Looping
CCS Spring 2013
4. ECONOMICS
Flue gas CO2 capture using a Ca-based chemical looping system has shown to be cost-competitive with the traditional amine-based systems in bench-scale testing (MacKenzie et al., 2007). Calcium looping provides several economic benefits, including the use of fluidized bed reactors (a technology proven at large scale), a cheap and abundant environmentally-benign sorbent derived from limestone and dolomite precursors, and the relatively lower energy efficiency penalty imposed on the industrial process (Dean et al., 2011). The most common CO2 capture technology on the market, amine scrubbing, imposes an energy efficiency penalty of 9.5 - 12.5%, while calcium looping only imposes an efficiency penalty of 6 - 8%. Furthermore, recent studies have estimated calcium looping to be more cost-effective than amine scrubbing in terms of tons of CO2 captured. Using a 360 MW PFB combined cycle power plant constructed in a western Canadian location, a 30-year levelized cost of approximately 22 USD/ton CO2 captured was estimated for calcium looping (MacKenzie et al., 2007). This value compared favorably to costs of 37.50 - 92 USD/ton CO2 captured by amine scrubbing. Costs were converted from Canadian to US dollars, and were inflated to portray 2013 prices. The range of costs for amine scrubbing reflects a literature search conducted to determine an accurate cost.

Calcium looping also presents a number of co-benefits. First, heat released during the carbonation step and heat generated in the calcination step can be directed to the steam cycle to increase overall plant efficiency. Second, there is potential for significant cost reductions in the production of hydrogen from fossil fuels coupled with CO2 capture. Finally, spent sorbent can be recycled and used in cement production, potentially decarbonizng not only power generation, but cement manufacturing as well.












Figure 4.1: Process of cement production

Figure 4.1 above depicts the basic process of cement production. Limestone undergoes calcination to produce CaO. Then, clay and a variety of additives (e.g., SiO2, Al2O3, Fe2O) are mixed with the CaO and heated in a kiln at 1400 - 1500 Celsius to produce clinker (Alsop et al., 2007). The clinker is cooled, and then a small amount of gypsum is added before it is placed into a grinder. The resulting material is cement, which is a main component of concrete. About 3.1 GJ of energy is required to produce 1 ton of clinker. However, if spent CaO from calcium looping is used, the energy required could be reduced by as much as 50% (Dean et al., 2011). Additionally, the raw material costs for cement production is greatly reduced, and waste disposal from the CO2 capture process at a power plant is eliminated. One potential drawback to using spent CaO in cement production is its affinity for SO2. A proportion of the CaO in the waste material will be in the form of CaSO4. ASTM C150 only allows for a maximum of 2.5% of sulfur in portland cement, because beyond this amount expansion and cracking of the cement paste can occur upon hydration (Dean et al., 2011).

A calcium looping sensitivity analysis is presented below in Figure 4.2. The parameters of caclium looping can be analyzed to determine which factors are most cost sensitive.






















Figure 4.2: Calcium Looping Sensitivity Analysis

It is clear that the dominant variables are related to the use or cost of the sorbent. These four variables are the cost of limestone, the Ca/C ratio, CaO deactivation rate, and CaO recycle rate. With respect to the cost of the limestone-based sorbent, negotiations will result in a market-driven charge to supply the limestone, and there will be limited scope to decrease this cost over time. The CaO recycle rate is assumed to be 92.5%, and this maximized rate is unlikely to increase. Perhaps it would be more advantageous to reduce recycle flow, which would decrease the cost of recycling large volumes of waste material through the combustor and calciner (MacKenzie et al., 2007). The best hope of improving calcium looping economics is either an increase in the efficiency of the Ca/C ratio, or a decrease in the CaO deactivation rate.


References:

[1] Alsop, P. A., Chen, H., Tseng, H., 2007. The Cement Plant Operations Handbook, Fifth Edition, Tradeship Publications, Surrey, UK. Chapter 17.
[2] Blamey, J., Anthony, E. J., Wang, J., & Fennell, P. S. (2010). The calcium looping cycle for large-scale CO2 capture. Progress in Energy and Combustion Science, 36(2), 260-279.
[3] Dean, C. C., Blamey, J., Florin, N. H., Al-Jeboori, M. J., & Fennell, P. S. (2011). The calcium looping cycle for CO2 capture from power generation, cement manufacture and hydrogen production. Chemical Engineering Research and Design, 89(6), 836-855.
[4] MacKenzie, A., Granatstein, D. L., Anthony, E. J., & Abanades, J. C. (2007). Economics of CO2 capture using the calcium cycle with a pressurized fluidized bed combustor. Energy & fuels, 21(2), 920-926.

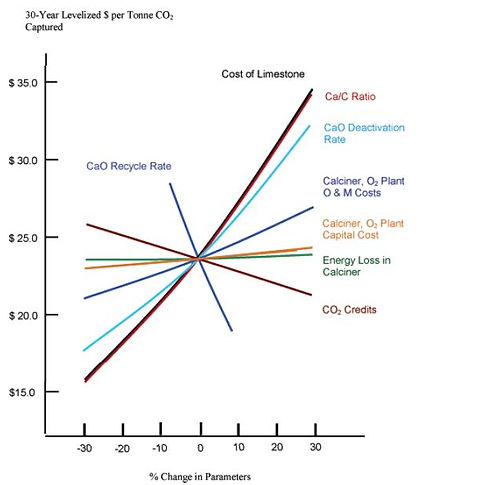